Design and construction with BIM for industrial facilities – Blue Projects Experience
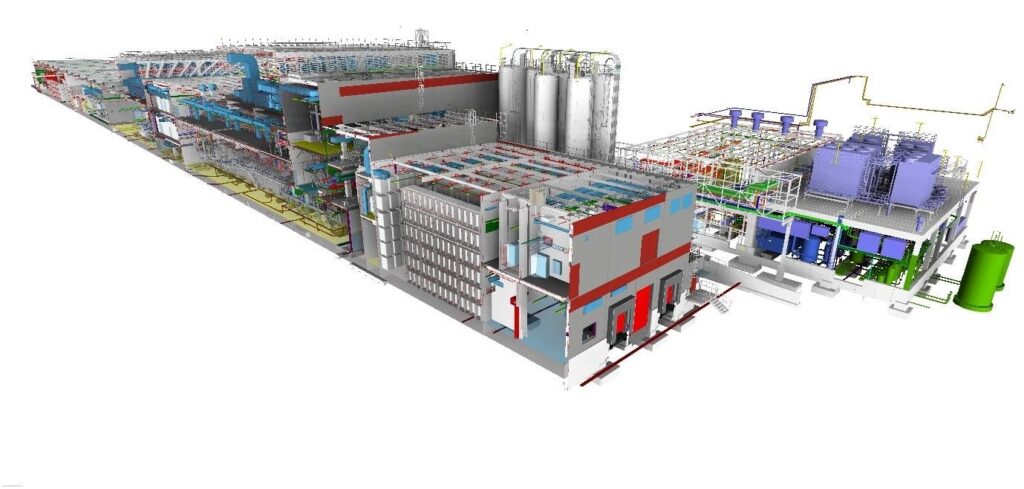
By Michał Zając, BIM Manager
Construction of large-footprint buildings dates back to the first industrial revolution. Since its onset in the 18th century the world has been seeing the emergence of more and more innovative solutions designed to facilitate the process of manufacturing and storage of goods. Broadly speaking, industrial buildings are structures, large in terms of cubic volume and floor space, that are designed to “enclose” this process.
Over the period of the last 200 years, in parallel to the development of construction technologies, industrial construction evolved from historic brickwork buildings to modern structures assembled of prefabricated elements and enclosed with sandwich panels.
What remains the same is the general division of the technology into process areas, packaging lines, warehousing areas and utility section, including chilled water, water vapour and compressed air systems. Industrial construction is distinguished from other sectors by specific process and equipment related requirements. These process and equipment related requirements define the design assumptions relating to architecture, construction and the building systems, including ventilation, power supply and fire protection. Adequate combination of these elements is also closely related to the specific features of the manufactured or stored goods.
Working at the interface of two different environments, namely civil engineering and technology we are faced with much greater demands relating to the design assumptions and to the coordination process, as compared to residential construction or commercial facilities, such as shopping centres.
Building information Modelling (BIM), a process of creation of a database in a 3D model is an ideal tool for efficient process of design and coordination in industrial construction and a right response to this challenge.
An example of projects where Blue Projects used the BIM technology is alteration of the Kellogg’s snack factory in Kutno, Poland. The scope included design of the manufacturing part of the premises, including construction and expansion of the following structures with the total floorspace of 21,000 sqm:
- Main production building with finished goods warehouse, raw material warehouse, in-plant offices and associated infrastructure, including waste management canopy, silos for dry products and spillage bunding with oil storage tanks.
- Utilities building including:
- air filtration system
- nitrogen station
- boiler house
- chiller plant and compressor building
- transformer station
Our responsibility in this project covered the full scope of Engineering, Procurement and Construction Management (EPCM), i.e. design, including procurement, and supervision of construction.
The BIM methodology and technology were among the main criteria applied during selection of the general contractor and are currently used at the detailed engineering and construction stages of the project.
Completion of construction was scheduled for December 2020.
For effective utilisation of BIM – in particular for industrial facilities – it is important to compile correct assumptions in the BIM Execution Plan (BEP in short).
BEP should be attached to the contract executed between the Owner and the Contractor and should reflect the specific features of the project defined by the type of the structure in question, developed with the use of BIM.
Depending on the Owner’s requirements BEP should be prepared on the basis of publicly available international guidelines or tailored to the Owner’s standards.
First of all, it must define the stages of the project, for which the model will be used, and its area(s) of application – co-ordination, take-offs, or scheduling of the works.
One of the key points is to correctly define the accuracy level of the model, as appropriate for the respective stages of the project. This is achieved by means of the Model Production Delivery Table (MPDT), which considers the information on the geometric accuracy and the numbers of parameters assigned to the different elements.
Without correct assumptions concerning, for example, clear zones, i.e. specification of the required clearances between objects such as ventilation ducts and pipelines we will not be able to correctly design these elements. Consequently, our work will be erroneous right from the start and effective routing of the pipelines and design coordination will become more and more difficult in the course of the project.
It is important to determine the number of models, as appropriate to the works or part of the process and equipment design and define their correct spatial relations. These are just a few examples from among the numerous points that should be included in the BIM Execution Plan.
What distinguishes industrial facilities from other, for example residential developments, are frequent alterations or expansions. This natural process can be necessitated, for example, by improvements to the process lines or result from expansion of the premises, as needed in relation to the growth of the company.
Typically, Owners employ various design firms over the years. Therefore, the risk of losing the data or their inconsistency, which can occur in the long run, must be taken into account by the manufacturing establishments. Each subsequent project related to modification of the existing situation must be based on the Owner’s materials and the available building survey reports. After 30-40 years of operation, the availability or status of the documentation may not be sufficient for the needs of a subsequent alteration or expansion project.
The 3D Terrestrial Laser Scanning and BIM technologies can be useful in such cases. Terrestrial Laser Scanning (TLS) is a non-intrusive measurement technique, in which laser technology is employed to measure the distance between a given point (for example the wall) and the laser scanner. The output of these measurements is a set of points in xyz-space, which compose the virtual image of the measured object, called a 3D point cloud. The use of the 3D scanner image as a reference material for design and spatial analysis considerably improves coordination and design process efficiency. The advantages of this measurement method include short time and high accuracy. Besides being much faster and more accurate than the conventional building survey techniques it also enables superimposing the texture from the photographs made during the survey on the obtained 3D image of the object. In this way a colour 3D scan can be obtained. A colour 3D scan is particularly useful for visual identification of utilities that are typically closely spaced in industrial premises. In addition, the most up-to-date spatial data become available and now we know what and how should be dismantled and what modifications should be made to the existing systems or process lines in question.
This technique was applied by Blue Projects at the design and development stages of its project consisting in alteration and expansion of the packaging production and warehousing building located also in Kutno.
The scope of design covers alteration and expansion of a factory building remaining in operation by adding to it the warehousing part, independent wash and toilet facility and canteen alteration. The project will increase the floor space by 6,500 m².
The 3D scan improved the efficiency of various design aspects, including co-ordination of the new structural details with the existing building.

